Before you buy air compressor system, you should know that temperature plays a bigger role in air compressor performance than you might think.
Air compressors are often subject to temperature extremes, especially if they are installed outdoors or in a warehouse without temperature controls. Large swings in temperature can lead to air compressor overheating in the summer or freezing in the winter. Understanding the optimal operating temperature for your compressed air system will help you avoid heat- or cold-related damage to your air compressor, ease the compressed air system maintenance, and extend the life of your system.
Air Compressor Operating Temperature Range
The optimal temperature range for your air compressor is fairly similar to the ideal temperature range for humans. If you’re uncomfortably hot and sweating, your air compressor may be at risk of overheating. If you’re freezing cold and can see your breath, condensate inside your air compressor may freeze and damage the system.
But how hot is too hot, and how cold is too cold? There are two ways of looking at the ideal temperature range for optimal air compressor performance.
Temperature Issues for Air Compressors: Hot vs. Cold
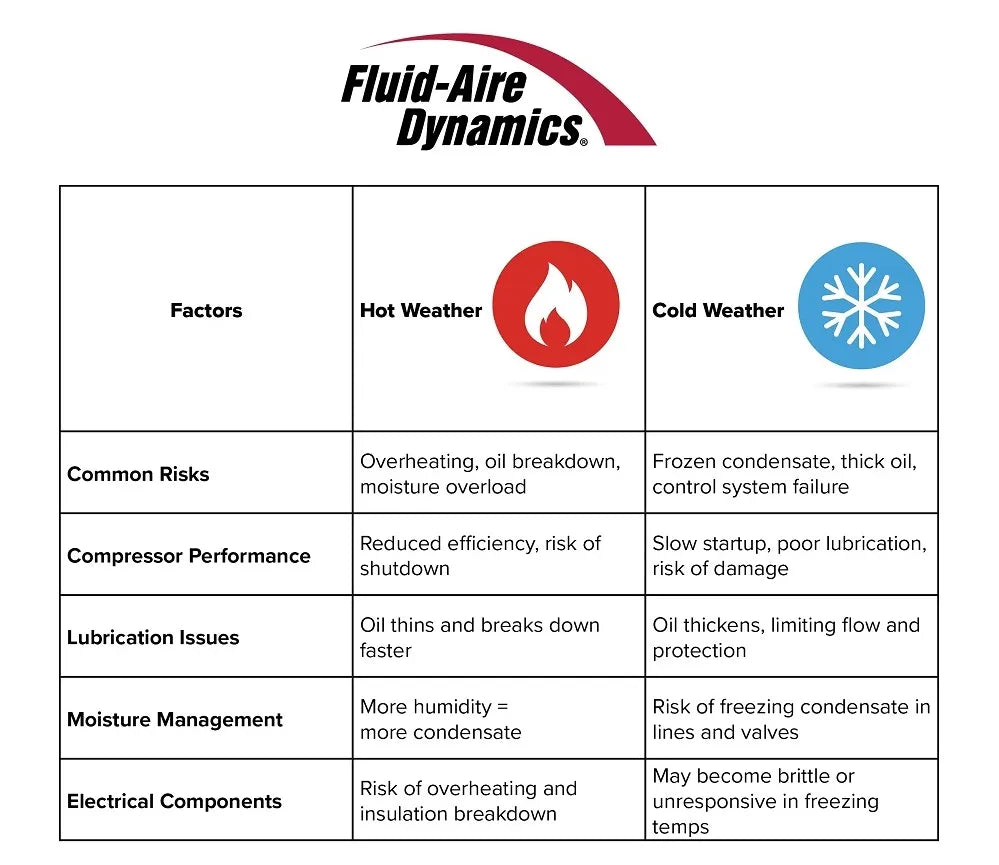
Optimal Temperature for Air Compressor Mechanical Performance
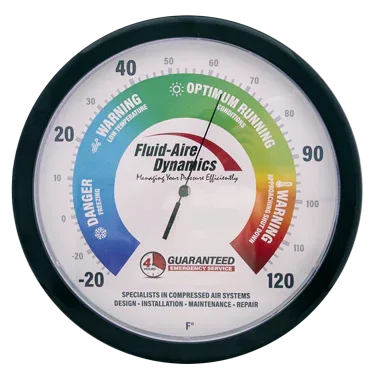
The ideal operating temperature for an air compressor is between 50 and 85 degrees Fahrenheit. Within this range, mechanical components are not at risk of freezing or overheating due to ambient conditions. Most compressor manufacturers engineer their machines for a maximum of 105°F, which is the max rating of the motor insulation. Maintaining ambient temperatures at 85°F or below will help to ensure that temperatures inside the machine stay below the 105°F max. Keeping temperatures within the 50–85°F range will also help your system run at maximum efficiency.
Air Density and Humidity
Within that range, cooler air is better. That’s because cool air tends to be drier — it can’t hold as much moisture as warm air. Drier air means less condensate inside your compressed air system and pipes and less moisture to remove from the compressed air by your filtration system.
Learn more: Getting rid of moisture in your compressed air system.
Operating Your Air Compressor in Cold Weather

Can you use your air compressor in cold weather? Cooler air may have less moisture, but there is a limit to how cold you want your system to get. Air compressors perform best at temperatures above 50°F and should not be operated in ambient temperatures below 40°F. Running your air compressor in cold ambient temperatures can lead to damage from condensate freezing inside the system. Furthermore, when a compressor is fired up from a cold start, the oil is thick. If it’s too thick, it may not deliver the flow necessary to provide the appropriate lubrication, leading to accelerated wear.
Frozen Condensate in the Air Compressor
At colder temperatures, condensate can freeze inside the air compressor or in the filters, pipes, drain valves and other components of your condensed air system. Ice will obstruct the flow of air and water through the system. Because water expands as it freezes, ice can also crack system components. This damage can be very expensive to repair. Ice in control lines will interfere with pressure controls, possibly causing over-pressurization or no pressure at all.
Cold-Proofing Your Air Compressor
If the ambient temperature in the area where the air compressor is located cannot be kept above 40°F, you may be able to install trace heating around pipes, an internal heater for your air compressor, and insulation to maintain safe operating temperatures inside the air compressor.

Cold Weather Air Compressor Maintenance
You should also be prepared to do some extra maintenance when operating your air compressor in cold weather. Check the air compressor and components daily for moisture and ice buildup, especially components that are far from the motor. Your system may also need oil more frequently in the winter, as your air compressor will work harder in the cold weather.
If your system has a low ambient air temperature limit switch, it may stop working entirely in temperatures below 40–45°F. In this case, you will need to bring the ambient temperature around the air compressor up to 45°F before restarting it.
Learn more: Can you use your air compressor in cold weather?
Operating Your Air Compressor in Hot Weather

Hot weather brings its own challenges for your compressed air system. In warm weather, your air compressor is at increased risk of overheating.
When it comes to hotter temperatures, most rotary screw compressors are designed to run up to internal temperatures of 105°F, which is the maximum temperature of class F insulation used in many electric motors.
There are three catches with running your air compressor in an environment this hot:
- The oil cooler must be perfectly clean.
- The oil sump tank must be filled to its maximum level.
- Premium quality fully synthetic oil must be used.
If the criteria above are not met, it is very likely that the machine will shut down in high ambient temperatures. Maintaining ambient temperatures of 85°F or below will reduce the risk of shutdown due to overheating.
Air Compressors for Hot Environments
If you have a hard time avoiding high temperatures, there are machines that can stand the heat (pun intended). Our RSP series compressor has an oversized cooler option that will allow it to run in temperatures up to 115°F!
Operating Air Dryers in High Temperatures
Another consideration in hot weather is the use of air dryers. Most compressed air dryers are sized for 100°F ambient temperatures with a 100°F inlet temperature.
In general, compressor air coolers are designed with a 15° approach. This means that if the ambient temperature is 85°F, the incoming air from the compressor to the dryer will be 100°F at full load. This is why we say 85°F is the ideal maximum temperature. If keeping temperatures below 85°F is not realistic, you may need to install a larger dryer to compensate for high temperatures.
Is Your Air Compressor Overheating?
Air compressor overheating is one of the most common causes of system failure. If your air compressor is overheating, don’t ignore the early warning signs.
Indicators that your air compressor is running hot include:
- Shutting down during high loads
- Frequent circuit breaker tripping
- Needing more time to reach peak operating performance
- System requires longer rest periods between cycles
- Smell of burnt oil
- Accelerated wear and frequent performance issues
Air Compressor Overheating: Causes
Overheating can be due to external conditions, internal problems within the air compressor, or a combination of both.
Some of the most common internal causes of air compressor overheating include:
- Dirty or blocked oil filter
- Blockage of oil cooler
- Failed fan
- Low sump oil level
- Thermal valve failure
Environmental conditions that lead to air compressor overheating include:
- Inadequate ventilation around the compressor
- High ambient temperatures
- Positioning the compressor next to heat-generating equipment
Air compressors are more prone to overheating as they age and system components start to wear. Pushing your air compressor beyond its normal capacity will also make overheating more likely. If your system is overheating frequently and seems to be aging too quickly, that may be a sign that you need a larger air compressor to meet compressed air demand for your facility.
Air Compressor Overheating: Solutions
There are several steps you can take to prevent air compressor overheating.
- If possible, control the ambient temperature in your air compressor room to maintain temperatures at 85°F or below. If this is not possible, avoid overloading your system with excessive demand when operating at high temperatures.
- Check the oil levels and change compressor oil on a regular basis. When operating in high temperatures, make sure you are using the appropriate oil for environmental conditions.
- Check the thermal valve to make sure that it is functioning properly. You might want to keep a spare on hand so you can swap it out to see if it is operating correctly.
- Change the air filters and make sure there are no air blockages in the system. Keep oil cooler coils (and all system components) clean.
- Improve ventilation in the compressor room and make sure there is adequate room for airflow around the compressor. Check ductwork for blockages, punctures, or debris buildup and clean vents and ductwork on a regular basis.
- Perform all recommended preventative maintenance. Replace parts that appear to be worn or are not operating at optimal capacity.
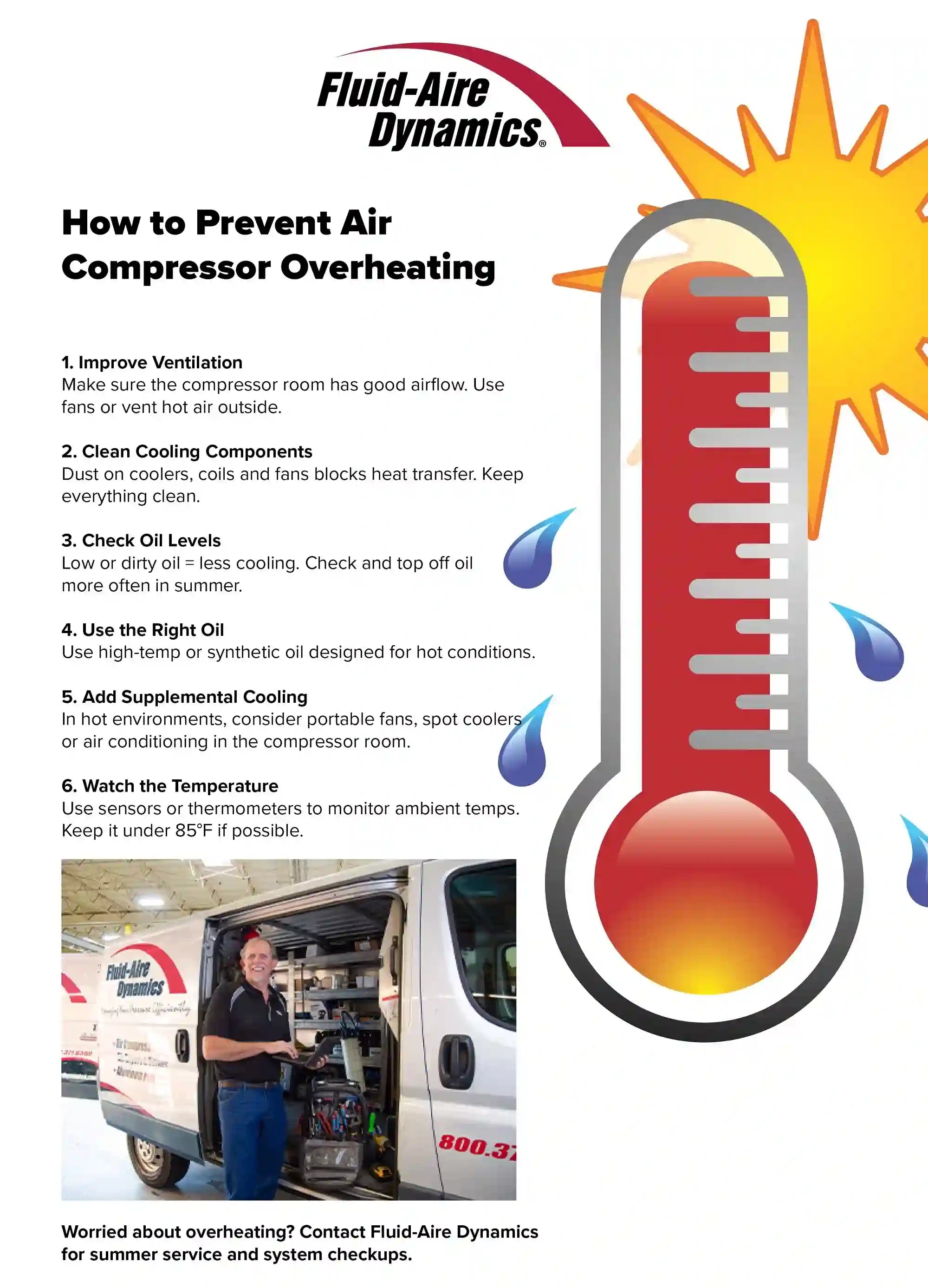
Maintaining Your Air Compressor in All Seasons
If your air compressor is subjected to temperature extremes, be prepared to perform some extra maintenance to keep it running in optimal condition year-round. If you’re not sure how to weatherproof your system, give the experts at Fluid-Aire Dynamics a call. We can help you design a compressed air system that will withstand your environmental conditions.
Need assistance? Give us a call!
847-678-8388
info@fluidairedynamics.com