Compressed Air Systems for Pharmaceutical Manufacturing
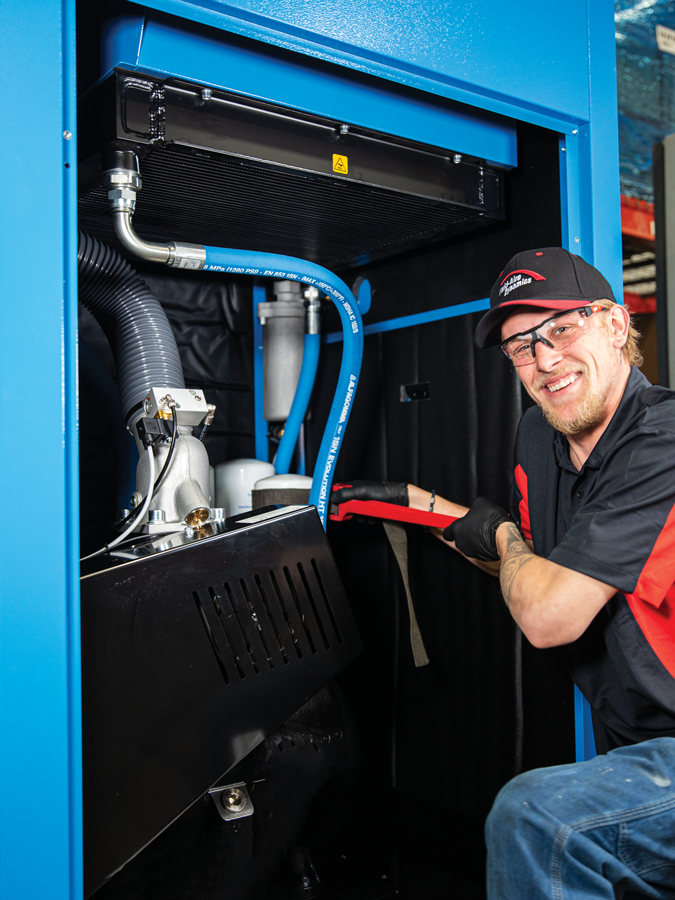
Where Is Compressed Air Used in the Pharmaceutical Industry?
Compressed air is used throughout the pharmaceutical manufacturing industry. Its primary application is for powering manufacturing equipment such as conveyors, tablet presses, mixers, weighing and measuring machinery, and packaging lines. But air is also used in ways that bring it in direct contact with ingredients, such as:
- Blow-off/cleaning of equipment and conveyors
- Drying and hardening
- Tablet coating
- Gel cap manufacturing
Compressed Air Standards for the Pharmaceutical Industry
The pharmaceutical industry is among the most regulated industries in the world. Pharmaceutical and nutraceutical manufacturers must follow stringent guidelines for cleanliness to keep the final product pure and contaminant-free. That includes ensuring that contamination does not make its way into production areas and final products via compressed air.
Compressed air use for pharmaceuticals and nutraceuticals can be broadly classified into two categories:
- “Direct contact” applications (like drying and hardening).
- “Indirect contact” applications (like powering production machinery and conveyors).
Air used in the pharmaceutical industry must be clean, dry and oil-free. Purity requirements depend on whether the application is considered a direct-contact application or an indirect-contact application. But even air used for indirect applications such as powering conveyors and packaging lines must meet basic purity standards for pharmaceutical applications. This is because small air leaks in the distribution lines or pneumatically powered equipment can introduce contamination into the surrounding environment. This contamination can end up in the final product and put the manufacturer out of compliance with cleanroom standards. For this reason, air purity is an important consideration for all compressed air applications in pharmaceutical and nutraceutical production.
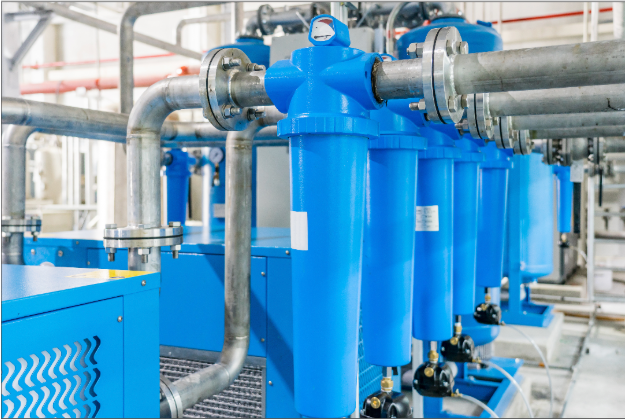
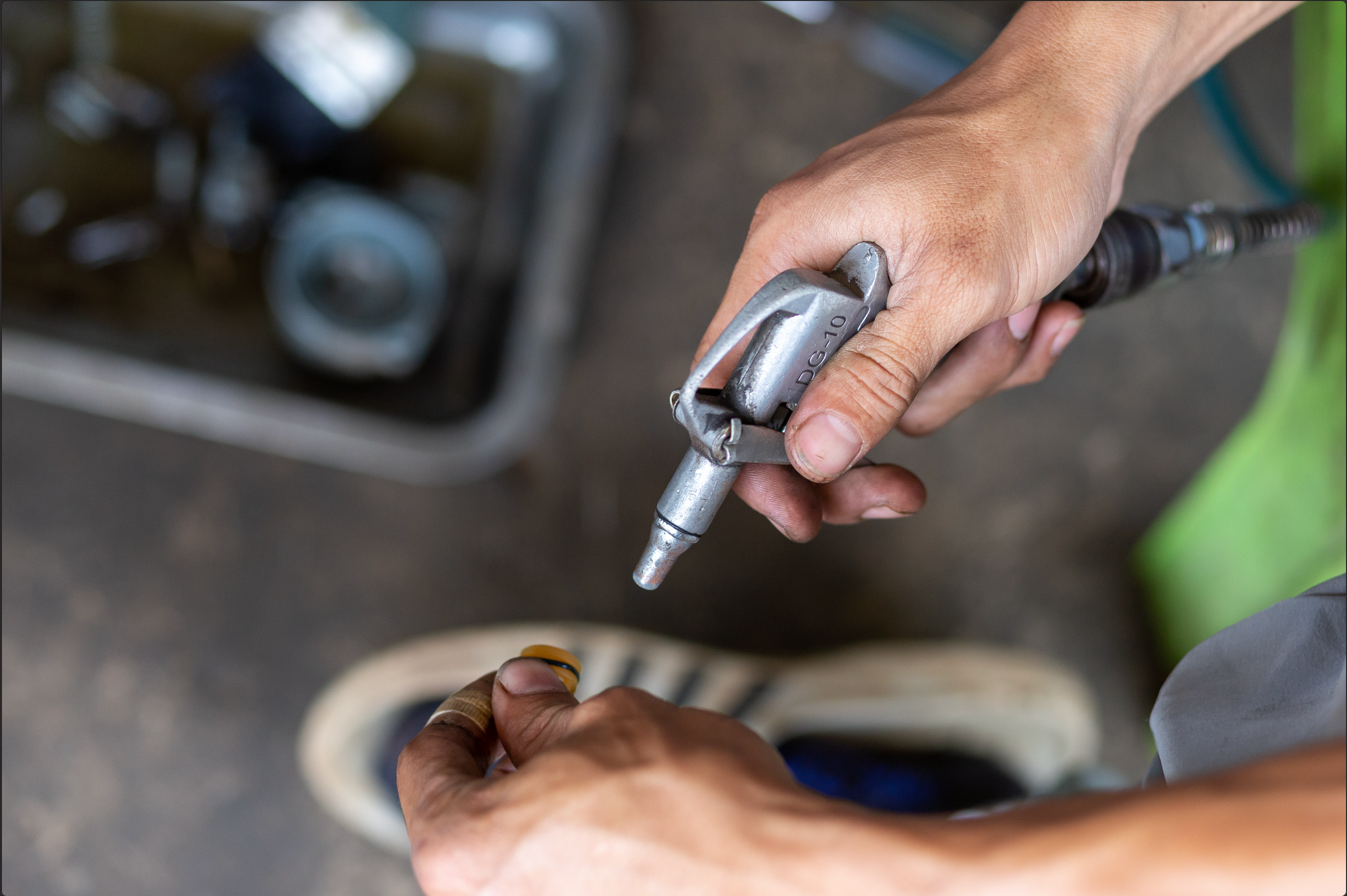
What Kind of Contaminants Are in Compressed Air?
Compressed air contaminants are categorized as dry particles, water and water vapor, and oil mists and vapors. All of them can cause problems for pharmaceutical and nutraceutical production.
- Particles include pollen, dust and microbes, such as mold spores and bacteria. Some of these make their way into compressed air through intake air: e.g., diesel fume from equipment running in the compressor room, airborne contaminants from manufacturing processes, and outdoor contaminants such as pollen and mold. Other contaminants may come from inside the compressed air system itself, such as rust from the air distribution system or particulate generated by the compressor through component wear. Any type of particulate contamination can be a problem for pharmaceuticals, which are held to very tight purity tolerances. But microbial contamination can be especially pernicious if mold or bacteria end up in environments that support their growth.
- Water is a natural byproduct of air compression. As ambient air enters the compressor through the intake, humidity in the air is squeezed out as liquid water, which ends up in the air supply. The amount of water entering the system depends on the temperature and humidity level of the ambient air. Water in the compressed air system can lead to corrosion inside ductwork or air-powered equipment, which in turn creates rust particles. But moisture is also a significant concern for pharmaceutical products that must be manufactured and stored in humidity-controlled environments. Excess moisture in compressed air may interfere with drying and hardening processes for tablets and gel caps or introduce product-damaging moisture into packaging.
- Oil carryover refers to the concentration of oil in the compressed air supply, which may be in the form of liquid droplets, aerosol mists or vapors. When using an oil-flooded air compressor, oil from the compressor can end up in the air supply. However, even oil-free compressors may have a certain amount of oil contamination from the intake air. Oil aerosols from production machinery or vehicles can end up in the ambient air of the compressor room; from there, they are introduced into the compressor. Oils and lubricants can create significant product quality issues for pharmaceutical and nutraceutical products.
Elevate Pharmaceutical Production with Reliable Air Systems
Contact Fluid-Aire Dynamics today for custom compressed air solutions designed to meet the highest pharmaceutical industry standards.
Compressed Air Standards for the Pharmaceutical Industry
It is important for pharmaceutical companies to select the right air purity class for their application. This will depend on questions such as:
- Does the air come in direct contact with products or product packaging? Any processes where air comes in direct contact with pharmaceutical products or final packaging must meet the highest purity standards.
- How important is humidity control for the application? Dry processes (such as tablet drying or processing) will be less tolerant of moisture in compressed air than wet processes (such as mixing lotions and balms).
- Does manufacturing happen in a cleanroom environment? For these applications, compressed air must meet the standards for the cleanroom classification level the process uses.
Compressed air quality is classified using metrics created by the International Standards Organization (ISO). ISO 8573-1:2010 lays out purity classes for compressed air according to the concentrations of particles, oil and water in the final product.
ISO has specifications for each type of contaminant.
- [A] Dry Particulate.
- [B] Humidity and Liquid Water.
- [C] Oil Total Concentration (aerosol, liquid and vapor).
Air is rated for a purity class for each contaminant type in an [A]:[B]:[C] format. So, if air is classified as purity class 1:2:1, that means that it meets Class 1 requirements for dry particulate and oil and Class 2 requirements for water. Class 0 compressed air is the cleanest; it must exceed Class 1 quality criteria and meet application-specific criteria (e.g., cleanrooms).
ISO 9573-1:2010 does not specify which purity classes must be used for specific applications; it is simply a method of classifying and comparing compressed air quality. The Food and Drug Administration (FDA) provides this guidance for pharmaceutical companies:
- “In cases where the gas is entering a classified area, it is required to at least meet the room classification limits established for the cleanroom environment”. (FDA Guidance for Industry: Sterile Drug Products Produced by Aseptic Processing – Current Good Manufacturing Practice, 2016).
- “Compressed gas should be of appropriate purity… and its microbiological and particle quality after filtration should be equal to or better than that of the air in the environment into which the gas is introduced”. (FDA Guidance for Industry: Sterile Drug Products Produced by Aseptic Processing – Current Good Manufacturing Practice, 2004).
In other words, compressed air used in manufacturing processes must equal or exceed air purity requirements for the manufacturing environment itself. For pharmaceutical applications that occur in a Good Laboratory Practice (GLP) environment and/or under cleanroom conditions, that will generally mean an ISO 8573-1:2010 class of 2, 1 or 0 for all three contaminant types. Pharmaceutical companies should perform due diligence to determine the right ISO 8573-1:2010 class for their specific application.
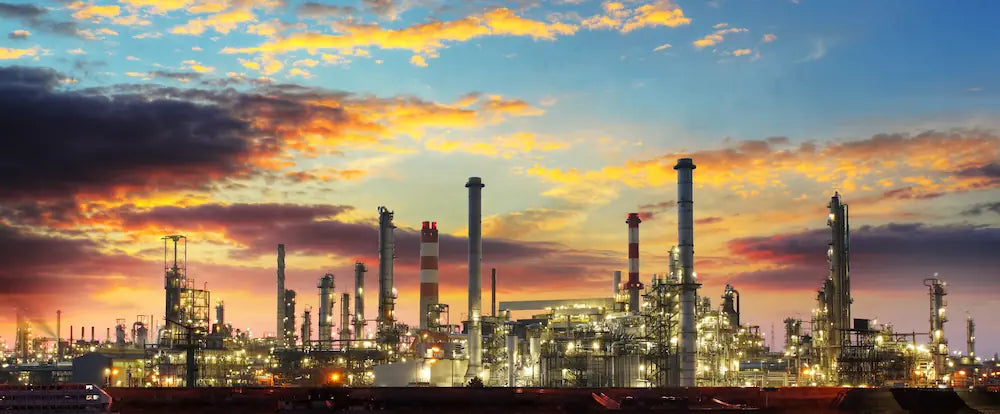
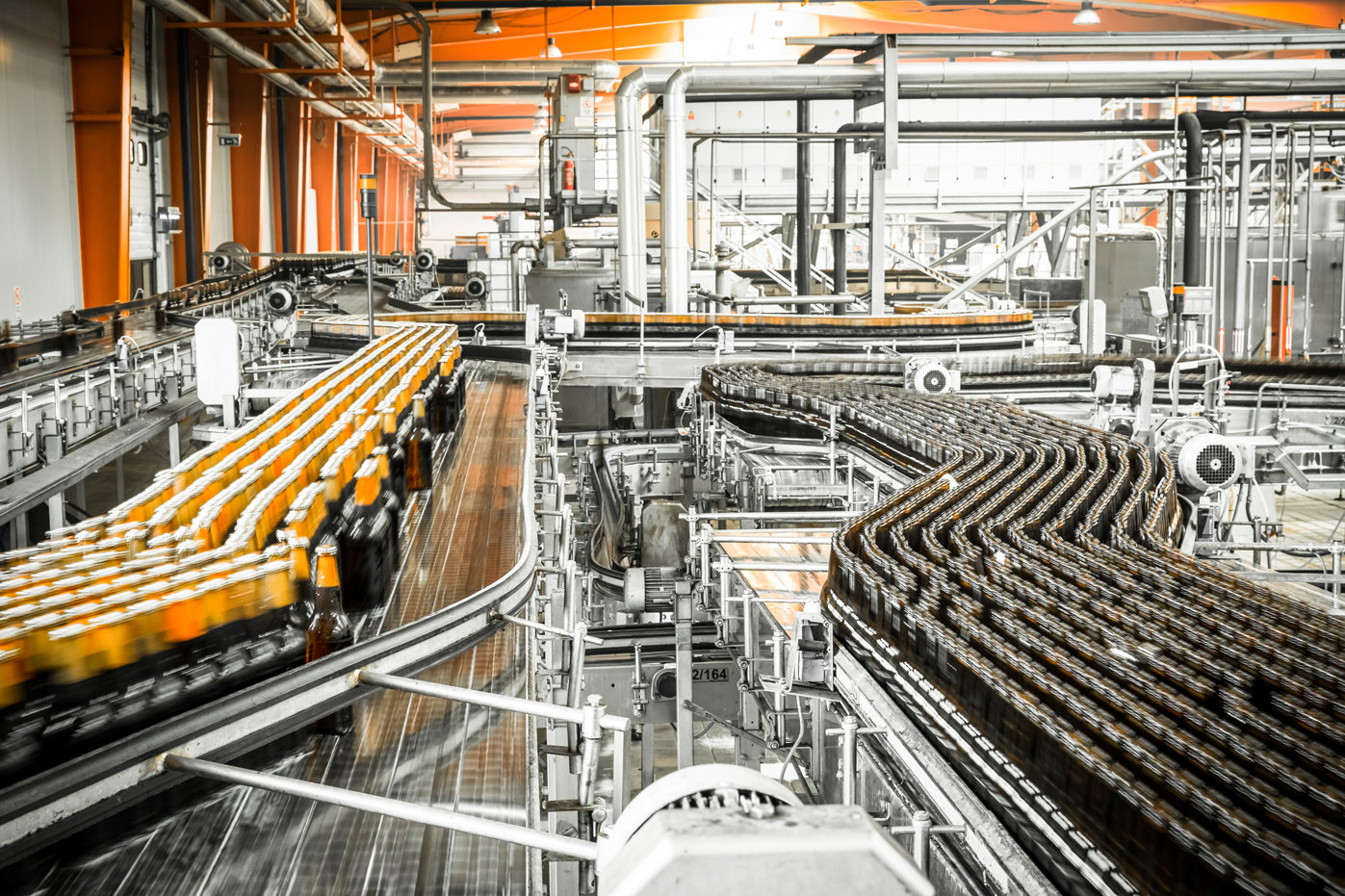
Is an Oil-Free Air Compressor Required for Pharmaceutical Production?
Many manufacturers assume that an oil-free air compressor must be used for pharmaceutical production. However, this is not always the case. In many cases, high-efficiency inline filtration, in combination with air drying, can produce compressed air with the purity levels required even for cleanroom applications.
An oil-free compressor uses rotors with very tight mechanical tolerances and a non-stick coating (e.g., Teflon) to reduce friction; air or water is used for cooling. In contrast, an oil-flooded rotary screw air compressor uses oil to lubricate and cool the rotors and provide a seal between the rotors and the walls of the air end. Small amounts of oil from the air end make their way into the compressed air supply (known as oil carryover); this oil must be removed via inline filtration.
In theory, an oil-free compressor will eliminate all oil carryover since there is no oil in the air end. However, while there is no oil carryover from the compressor, that does not necessarily mean there is no oil in the air. An oil-free compressor will not eliminate oil that enters the system through the intake air. Intake air can be contaminated by oil mists created by production machinery or vehicles operating in the vicinity of the compressor; if not removed, this oil will end up in the air supply. For this reason, inline filtration is usually still required even when using an oil-free air compressor.
An oil-free compressor is much more expensive to purchase and operate. An oil-free compressor may be as much as twice the capital cost of an oil-flooded rotary screw with the same CFM. And even with non-stick coatings, there is more friction on the rotors compared to an oil-flooded model, which significantly reduces the service life of the machine. Repairs can be very expensive for an oil-free compressor, as well. When you consider capital, repair and maintenance costs, along with the shorter service life of an oil-free compressor, it is almost always cheaper, in the long run, to go with an oil-flooded compressor and invest in high-efficiency filtration.
Today’s oil-flooded rotary screw compressors and oil separators are highly reliable. With good filtration, an oil-flooded compressor can provide problem-free, clean, dry and oil-free compressed air for years to come.
Achieving Air Purity Standards for Pharmaceutical and Nutraceutical Manufacturing
An oil-flooded rotary screw compressor with high-efficiency filtration and air dryers can remove nearly all dry particulate, oil and water to meet ISO purity classes of 2 or better. It is even possible to meet cleanroom requirements with the right filtration and drying equipment.
There are several steps to producing high-purity compressed air for pharmaceutical applications.
- Start with a good intake filter to remove large particulates and some oil mists from the intake air. This will reduce wear and tear on your inline filters. For the highest-purity cleanroom applications, the compressor itself can be kept in a cleanroom or enclosure with air filtration to prevent contaminants from the outdoors or production environments from reaching the compressor intake.
- Use an air dryer to remove water from compressed air. A refrigerated air dryer can get air down to a dew point of ~38°F, equivalent to an ISO 8573-1:2010 [B] Class 4. This may be alright for applications that are not moisture sensitive, but to achieve ISO 8573-1:2010 [B] Class 1, 2 or 3, you will need a desiccant air dryer. A desiccant dryer can achieve dew points as low as -40°F to -100°F, or ISO 8573-1:2010 [B] Classes 2 and 1.
- Use inline filtration to remove oil and dry particulates. A high-efficiency coalescing inline filter removes particulates down to 0.01 microns (ISO 8573-1:2010 [A] Class 1) with a maximum oil carryover of 0.008 PPM (ISO 8573-1:2010 [C] Class 1). Activated carbon inline filters also remove hydrocarbon mists, vapors and odors, with a maximum oil carryover of 0.002 PPM, which may meet even Class 0 requirements.
Aire Tip: Inline filtration should be used for cleanroom applications even when using an oil-free compressor to ensure that contaminants from intake air do not make their way into the air supply.
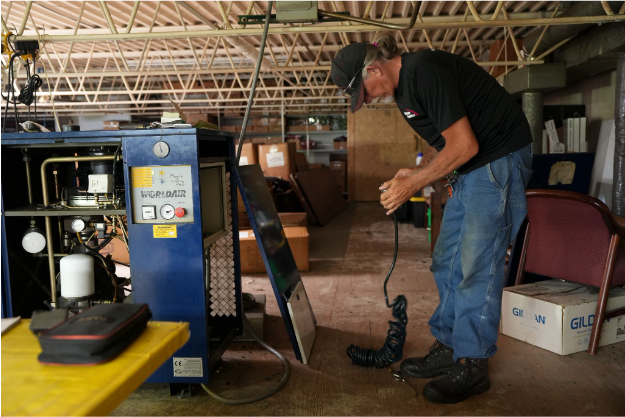
Why Choose Fluid-Aire Dynamics for Pharmaceuticals?
When it comes to pharmaceutical manufacturing, Fluid-Aire Dynamics offers unmatched expertise and clean air solutions designed to meet the industry's stringent quality and compliance requirements.
-
Pharmaceutical Expertise You Can Trust
With years of experience serving the pharmaceutical industry, we understand the critical importance of clean air systems. Our solutions are tailored to address the unique challenges of sterile manufacturing environments.
-
Regulatory Compliance and Quality Assurance
Our systems are designed to meet or exceed the strict standards set by the FDA, GMP, and ISO. We provide full documentation and support to ensure compliance at every stage of operation.
-
End-to-End Support
From initial design and installation to ongoing maintenance and emergency repairs, Fluid-Aire Dynamics offers comprehensive support to keep your operations running smoothly year-round.
FAQs About Compressed Air for Pharmaceutical Use
What are the risks of using non-compliant compressed air systems in pharmaceuticals?
Can you customize compressed air systems for specific pharmaceutical applications?
How does compressed air support cleanroom operations in pharmaceutical manufacturing?
How do nitrogen generators benefit pharmaceutical operations?
Optimize Your Pharmaceutical Air Systems Today
Let Fluid-Aire Dynamics help you enhance product safety, efficiency, and compliance with customized compressed air solutions. Contact us for a free consultation!