High-Performance Compressed Air Solutions for Aerospace, Military & Defense
Compressed Air Services for Aerospace, Military & Defense
Our tailored services are designed to provide unmatched reliability, efficiency, and precision for aerospace and defense operations.
Why Choose Fluid-Aire Dynamics for Aerospace & Defense?
Fluid-Aire Dynamics delivers precision-engineered compressed air systems that meet the demanding requirements of aerospace, military, and defense operations, ensuring reliability under the toughest conditions.
-
Proven Expertise in Mission-Critical Applications
With years of experience supporting aerospace and defense industries, we understand the stringent requirements and high-stakes nature of your operations. Our solutions are designed for absolute precision and reliability.
-
Custom-Engineered Solutions for Specialized Needs
We design systems tailored to your unique applications, from high-pressure testing to clean air delivery for sensitive manufacturing. Our solutions integrate seamlessly into your workflow, ensuring efficiency and compliance.
-
Comprehensive Lifecycle Support
From system design and installation to ongoing maintenance and emergency repairs, we provide full-spectrum support to keep your operations running smoothly year-round.
How Compressed Air Is Used in the Aerospace Industry
Compressed air is utilized extensively in the aerospace industry and defense sector to power tools and equipment, clean and prepare parts, power system controls, and test critical components and systems. Here are some common applications for compressed air systems in the aerospace field.
Aircraft Manufacturing
Aircraft manufacturing is a complex process involving numerous stages, and compressed air is an indispensable tool throughout these stages. Some of the most common applications include the following.
- Pneumatic tools: Compressed air powers a range of tools, such as rivet guns, screwdrivers, drills, and wrenches, which are critical for the assembly of aircraft parts. Air-powered shears and nibblers are used to cut and shape the sheet metal that forms the aircraft's body.
- Surface preparation and part cleaning: Before painting, coating, or metal finishing, surfaces need to be prepared. Air-powered sanders, grinders, and abrasive blasters are used for this purpose. Parts may also need to be thoroughly cleaned before assembly. High-pressure compressed air effectively removes contaminants, oil, or other residues from components.
- Painting and metal finishing: Compressed air is used for spray painting aircraft components, ensuring an even and smooth finish.
- Plastic molding: Compressed air can assist in the molding processes of various aircraft interior components, like overhead bins or seating elements.
- Aircraft engine manufacturing and engine cleaning: Jet engines and their components can be cleaned during their manufacturing process with compressed air to ensure that no residual contaminants are left that might affect performance. Compressed air may also be used for engine testing and cooling during aircraft engine manufacturing.
- Testing and quality control: Pressure testing is used to test essential components, especially those in the fuel or hydraulic systems, for leaks and durability. Compressed air is often used to apply this pressure. Compressed air may be used in cooling systems during rigorous avionics testing to replicate real-world conditions.
- Material handling and automation: Pneumatic actuators are used in automated systems to move or position parts during the manufacturing process. Some heavy components might be moved around the factory floor on an air cushion of compressed air, reducing friction and the risk of damage.
- Composite material production: Many modern aircraft use composite materials because of their strength and lightness. During the curing process of some composites, vacuum and pressure are applied, and compressed air can play a role here.
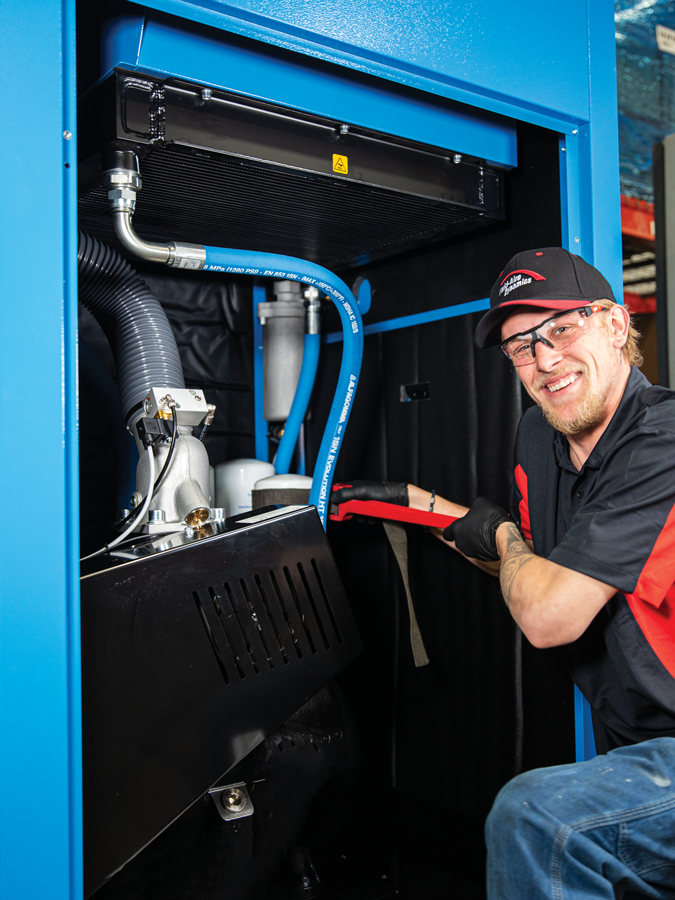
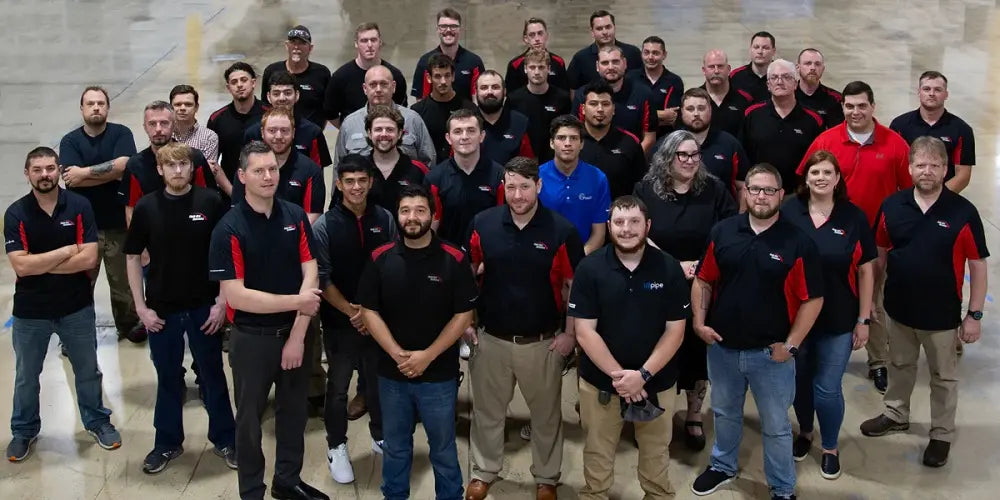
Aircraft and Heavy Equipment Maintenance
Compressed air plays an indispensable role in aircraft maintenance in both military and civilian realms, ensuring aircraft operate at their peak efficiency and safety. There are numerous applications of air compressors for aircraft maintenance and ground support equipment.
- Pneumatic tools: Compressed air is used for powering pneumatic tools such as drills, wrenches, and rivet guns.
- Engine cleaning: Compressed air can be used for cleaning engine components.
- Hydraulics and fuel lines: Pressure testing essential systems like hydraulics and fuel lines, ensuring they are leak-free and operational. Compressed air may also be used for fuel injection in some models of aircraft.
- Surface cleaning: High-pressure air blasts are used for surface cleaning, effectively removing debris, oil, and contaminants.
- Landing gear systems: Compressors may be used for testing and maintaining pneumatic components for landing gear.
- Other ground support equipment: Ground support equipment (GSE) encompasses a variety of other tools for aircraft tire service, cleaning, deicing, cabin air circulation, etc. Ground support equipment such as lifts and jacks may be powered by pneumatic air systems.
Missile and Weapons Systems
Air compressors are used by the defense industry for missile and weapons systems. Some applications include:
- Ejection mechanisms: Compressed air is used in some missile ejection systems from launch tubes or aircraft.
- Pneumatic controls: For certain guided missile systems and other weapon platforms.
Oxygen Generation Systems
In aviation, especially military aviation, onboard oxygen generation systems (OBOGS) may utilize compressed air as part of the process to supply breathable air to pilots, particularly during high-altitude or long-duration flights. These systems are designed to separate oxygen from the ambient air, supplying it to the pilots and potentially other crew members as needed. This air is then compressed using an onboard compressor, which is often integrated into the aircraft's engine system. The compression process raises the pressure of the air, making it easier to separate the oxygen from other gases.
Avionics Cooling
Compressed air can be employed to cool sensitive equipment in avionics, especially in military aircraft where reliability and performance are crucial and high temperatures prevail. Maintaining ideal operating conditions during flight is crucial for the optimal performance and reliability of electronic components and systems in high-performance aircraft. An onboard air compressor can be used to direct airflow at high-heat zones to ensure efficient cooling. Compressed air may also be used in systems for brake heat transfer. This rapid cooling can prevent overheating and prolong the life of the brake components.
UAVs (Unmanned Aerial Vehicles)
Compressed air can be used in the launching mechanism of certain drones or UAVs. Some UAVs, especially those deployed from naval vessels or ground vehicles, use compressed air catapult systems for launch. Onboard compressed air systems may also be used for pneumatic actuators, payload deployment, cooling, and emergency systems.
Secure Your Aerospace and Defense Operations with Reliable Air Systems
Contact Fluid-Aire Dynamics today for tailored air solutions designed to meet the rigorous demands of aerospace, military, and defense operations.
How Nitrogen Is Used in Aerospace and Defense
Nitrogen gas is extensively used in the aerospace and defense industries for a variety of applications, owing to its inert properties, low reactivity, and ability to reduce or eliminate the risk of combustion. On-site nitrogen generation can provide a steady supply of nitrogen for avionics. Here are some key uses for a nitrogen generator in the aerospace industry and defense applications.
Aircraft Manufacturing
- Inert Atmosphere: Nitrogen gas is used to create an inert atmosphere in certain manufacturing processes — such as welding, curing of composite materials, or certain heat treating or metal finishing processes — to improve the quality of the end product.
- Material Treatment: Processes like cryogenic milling use liquid nitrogen to keep materials at extremely low temperatures, allowing for easier manipulation and higher precision.
Aircraft Maintenance
- Aircraft Tire Inflation: Nitrogen gas is often used rather than air for the inflation of aircraft tires because nitrogen is less prone to expansion and contraction with temperature changes, which is crucial during take-offs and landings.
- Hydraulic Systems: Nitrogen is used as a backup or supplement for hydraulic systems in some aircraft.
- Shock Absorbers: Nitrogen is used in aircraft shock absorbers to provide the “spring” effect, returning the shock absorber to its original position after it is compressed.
- Leak Testing: Nitrogen gas is used for pressure testing fuel and hydraulic systems to check for leaks due to its inert quality.
- Oxygen Systems: Nitrogen can be used to purge and test aircraft oxygen systems to ensure they are free from contaminants before being filled with oxygen.
Fueling and Storage
- Fuel tank purging: Nitrogen can be used to purge the fuel tank to displace volatile vapors and inert the fuel tank prior to maintenance.
- Long-term Storage: Aircraft or equipment that is being stored for an extended period might have fuel tanks filled with nitrogen gas to prevent corrosion.
Ground Operations
- Fire Suppression: In areas where fire risk is a concern, nitrogen gas can be used as a fire suppression medium.
- Supporting Equipment: Ground support equipment, like mobile electric power generators or air conditioners, may use nitrogen in various capacities.
Avionics Safety Systems
Nitrogen gas canisters (sometimes in combination with CO2 gas) are used in high-pressure inflation systems for rapid inflation of aircraft slides and life rafts.
Military Applications
- Ammunition: Nitrogen gas is sometimes used in the manufacture of certain types of ammunition.
- Chemical, Biological, Radiological, and Nuclear (CBRN) Defense: Nitrogen can be used to create inert environments for the safe handling or deactivation of dangerous substances.
- Submarines: In submarines, nitrogen gas is sometimes used for fire suppression and to control the onboard atmosphere.
- Missile Systems: Nitrogen can also be used in the cooling systems of missile guidance electronics.
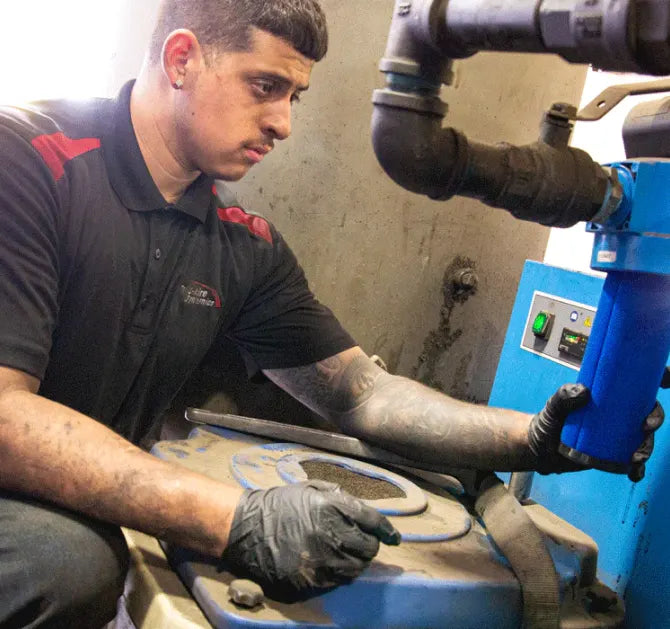
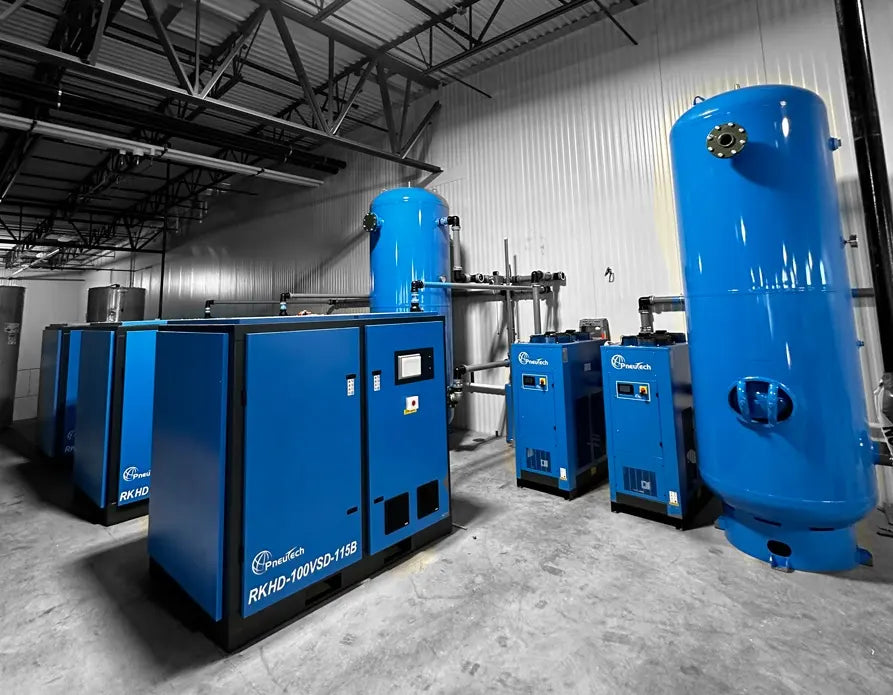
On-site Nitrogen Generation Equipment for Aerospace Applications
On-site nitrogen generation has significant benefits for the aerospace industry and defense industry in terms of cost savings, reliability, and operational flexibility.
- Cost-Efficiency: Traditional methods of nitrogen supply often involve transportation and rental fees, both of which can be mitigated by generating nitrogen on-site. Over the long term, on-site generation often proves to be a cost-effective alternative.
- Reliability: Having a nitrogen generation system on-site ensures a constant, reliable supply. This is crucial in aerospace and defense applications where the lack of a critical component like nitrogen gas can halt operations or compromise safety.
- Quality Control: On-site nitrogen generation allows for more precise control over the purity and pressure of the nitrogen, tailored to specific needs, whether it be for aircraft tire inflation, fire suppression, or sensitive equipment for avionics.
- Operational Flexibility: On-site systems can be scaled up or down relatively easily, allowing for greater responsiveness to changes in demand. This is particularly important in dynamic fields like aerospace and defense, where operational requirements can change rapidly.
- Reduced Logistics and Storage: Generating nitrogen on-site eliminates the need for storing large volumes of compressed or liquid nitrogen, reducing storage costs and safety risks associated with handling and storing high-pressure cylinders.
Readiness: In mission-critical scenarios, the availability of essential supplies like nitrogen can be the difference between success and failure. On-site generation ensures that nitrogen is always available when needed.
FAQs About Compressed Air in Aerospace & Defense
What standards must compressed air systems meet in aerospace and defense?
Can Fluid-Aire Dynamics provide solutions for high-pressure applications?
How does compressed air support ground support equipment (GSE)?
What maintenance is required for compressed air systems in military applications?
Optimize Your Aerospace and Defense Systems Today
Let Fluid-Aire Dynamics provide the reliable, precision-engineered compressed air solutions you need. Contact us for a free consultation!